Discover Iren’s groundbreaking facility in Tuscany, designed to recover gold, silver, palladium, and copper from e-waste. Learn how this innovative process supports the circular economy while reducing environmental impact.
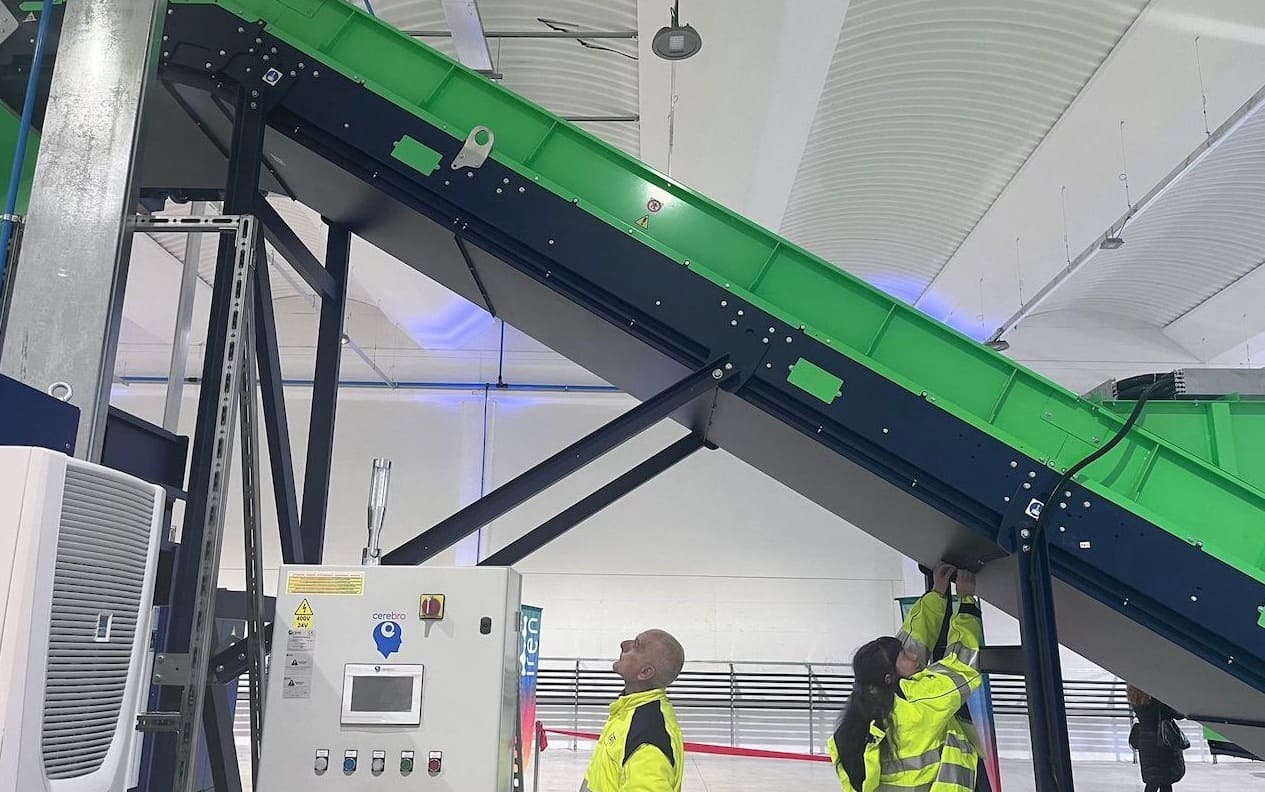
In a groundbreaking move for sustainability, Iren has inaugurated Europe’s first facility for recovering precious metals from electronic waste. Located in Terranuova Bracciolini, Tuscany, the plant has an annual processing capacity of over 300 tons of electronic circuit boards, recovering nearly 200 kilograms of precious metals and 57 tons of copper each year.
A Game-Changer in Precious Metals Recovery
The plant extracts gold, silver, palladium, and copper from Waste Electrical and Electronic Equipment (WEEE). Spanning 2,400 square meters, it represents a significant leap in Italy’s efforts to recover the mere 30% of electronic waste currently being processed correctly.
Innovative Technology for Precious Metals Extraction
Iren’s facility employs an advanced mechanical disassembly and hydrometallurgical treatment process. This innovative technology separates non-precious metals, followed by the recovery of precious metals and critical raw materials, all certified using blockchain.
The plant is capable of weekly recoveries, including:
- 1 kilogram of gold
- 2 kilograms of silver
- 0.5 kilograms of palladium
- 500 kilograms of pure copper
- 600–700 kilograms of copper powder
Over a year, this amounts to nearly 200 kilograms of precious metals and 57 tons of copper.
Ending the Export of Circuit Boards
Currently, over 90% of electronic circuit boards in Italy are exported. The new facility not only reduces this figure but also strengthens the local circular economy. The recovered materials can directly support the renowned goldsmith district in the area, eliminating the need for additional processing.
A Sustainable Approach
Luca Dal Fabbro, president of Iren, emphasized the project’s significance:
“With this plant, Iren introduces a new paradigm of sustainability in Italy. This milestone, achieved with the support of national and local authorities, aligns with our strategy of sustainable investments and value creation for the region. By choosing Tuscany for this facility, we aim to leverage the unique characteristics of Valdarno’s economic fabric.”
How the Plant Works
Step 1: Thermo-Mechanical Separation
- Circuit boards are analyzed using spectroscopic methods to assess quality.
- Boards are heated to 220°C to separate components, with the facility processing up to 1 ton per batch.
- This precise process surpasses traditional sampling methods used in incineration plants.
Step 2: Chemical Recovery and Refinement
The crushed components undergo two key processes:
- Leaching: Using two different acid solutions, non-precious metals like iron, lead, tin, aluminum, and copper are extracted.
- Refinement: Crushed components are processed in six reactors with specialized solutions to recover:
- Silver: Converted to silver chloride and molded into ingots.
- Gold: Purified into 24-karat ingots.
- Palladium: Recovered as a dissolved salt in liquid form.
- Copper: Refined through electrolysis.
Environmental Benefits
Recycling electronic waste through this facility reduces energy consumption and cuts CO₂ emissions by threefold compared to traditional mining. Moreover, the plant is designed with sustainability in mind:
- Water Reuse: Industrial water is treated and reused, minimizing discharge.
- Emission Control: Air emissions are tightly monitored with advanced filtration systems.