Developed by KRISS, the breakthrough material significantly improves green hydrogen production while reducing costs
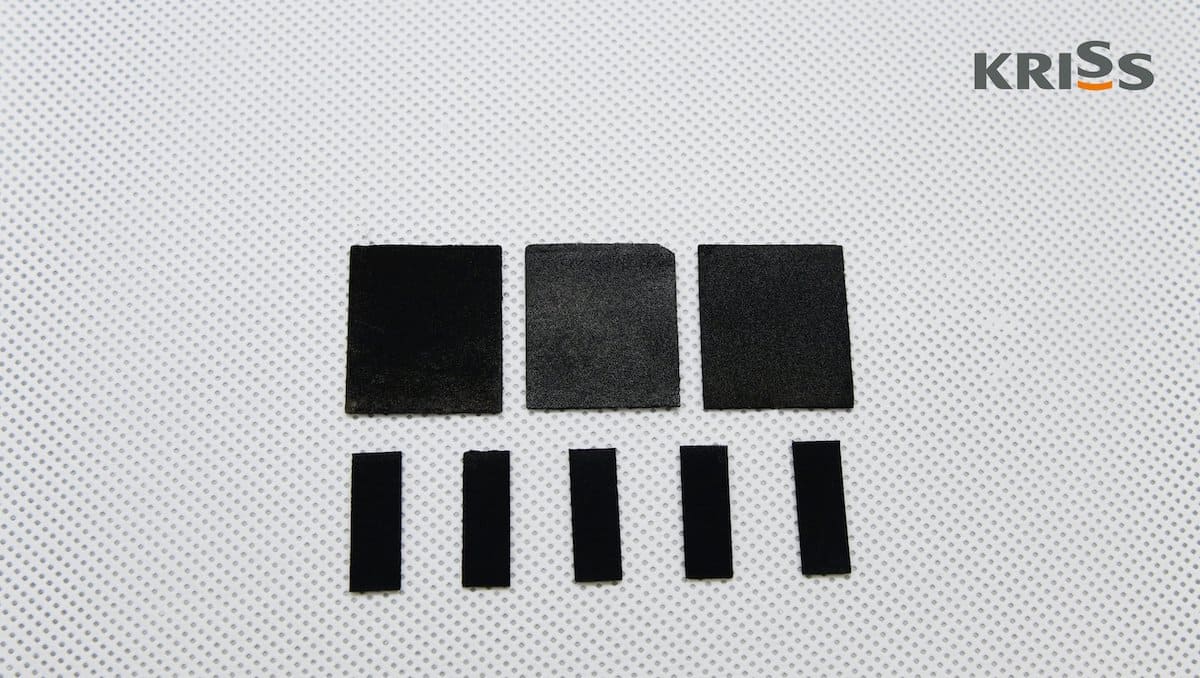
A groundbreaking innovation from South Korea’s Korea Research Institute of Standards and Science (KRISS) is set to enhance anion exchange membrane (AEM) electrolyzers. Researchers have introduced a molybdenum-based catalyst infused with ruthenium, designed to improve electrochemical stability. The result? A system capable of efficiently producing hydrogen from water—including seawater—for over 300 hours without performance degradation.
AEM Electrolyzers: How They Work and Why They Matter
AEM electrolyzers are one of three leading technologies for low-temperature hydrogen production from water. As the name suggests, they use a semipermeable membrane that transports hydroxide ions (OH−) to split water molecules into hydrogen and oxygen.
One of the biggest advantages of AEM electrolysis is its ability to function without expensive noble metal catalysts like platinum. Additionally, like alkaline electrolysis, it operates in a basic environment but with less stringent operating conditions, reducing risks and improving efficiency.
Recent studies have shown that molybdenum oxide-based electrocatalysts can rival the performance of platinum in hydrogen evolution reactions. This is due to their high conductivity, excellent hydrogen adsorption, and water dissociation capabilities.
However, a major challenge remains: most molybdenum oxide catalysts degrade too quickly under industrial conditions when current density exceeds 100 mA/cm². The primary issue is the adsorption of hydroxide ions on molybdenum dioxide, which accelerates catalyst degradation. This is where the KRISS innovation comes into play.
KRISS Catalyst: A Breakthrough for AEM Electrolysis
Scientists at KRISS’s Emerging Material Metrology Group have developed a new catalyst by introducing ruthenium (Ru) nanoparticles into a nickel-molybdenum oxide structure.
This nanoscopic ruthenium layer forms a protective shield over the catalyst, preventing degradation and significantly improving its stability and lifespan. In testing, the AEM electrolyzer with this novel catalyst operated stably for over 300 hours at a current density of 1.0 A/cm²—a crucial step toward industrial application.
According to the National Research Council of Science and Technology, “performance evaluations revealed that these newly designed catalysts offer four times the durability and over six times the activity of existing commercial materials.”
Moreover, when integrated with a perovskite-silicon tandem solar cell, the catalyst achieved an impressive solar-to-hydrogen efficiency of 22.8%, demonstrating strong compatibility with renewable energy sources. The study also found that the catalysts maintained high activity and stability in seawater, producing high-purity hydrogen without desalination, which could dramatically reduce hydrogen production costs.
The research has been published in Applied Catalysis B: Environment and Energy.