Green iron production via electrochemistry cuts emissions and costs. Porosity is key to scalable, sustainable steel manufacturing
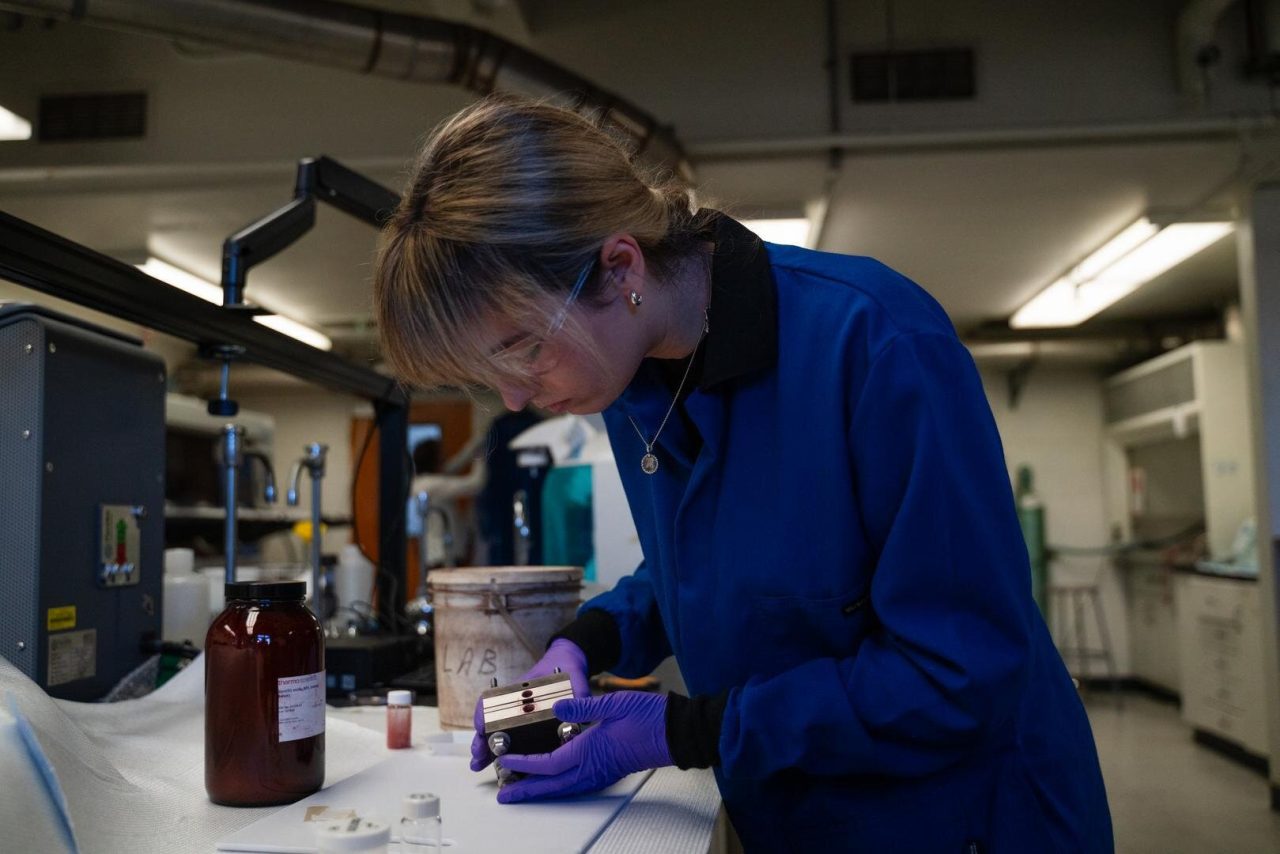
Electrochemical iron production: a zero-emissions path
Can green iron production reduce the environmental toll of steelmaking? A research team at the University of Oregon believes it can. They’ve developed a techno-economic model to assess the competitiveness of electrochemical iron production in terms of both cost and scalability.
This metal, essential for global steel manufacturing, is typically extracted by reducing iron oxides found in ores like hematite (Fe₂O₃) and magnetite (Fe₃O₄). After mining, the ore is crushed, ground, and purified before being fed into blast furnaces along with coke and limestone to produce pig iron. But pig iron is high in carbon and must undergo further processing to become steel, a versatile and durable material.
The conventional method is not only highly energy-intensive – requiring temperatures above 1,000°C – but also releases significant CO₂ as a byproduct.
The breakthrough in green iron research
The University of Oregon team published their findings in ACS Energy Letters, describing a zero-emissions process that uses electrochemistry to convert saltwater and iron oxide into pure metallic iron.
Their work identifies which types of iron oxides make the reactions more efficient. “We now have a chemical principle, a sort of design rule, that helps us identify low-cost iron oxides suitable for these reactors,” one of the authors explained.
When the team began testing the process, they experimented with various iron oxide sources and quickly noticed that some performed far better than others. However, they were unsure what caused the variation in metallic iron yield. Was it the oxide particle size? The material’s composition? Or specific impurities?
One step closer to green iron
To find out, the researchers ran a series of tests, converting iron oxide powder into nanoparticles. In one experiment, they discovered that heat-treated nanoparticles became denser and less porous.
That led to a key insight. “With highly porous particles, we can produce iron very quickly in a small area,” said co-author Andrew Goldman. “Dense particles don’t react as fast, which limits the amount of iron we can produce per square meter of electrode.” And production speed is critical to making the process economically viable.
According to the researchers, it’s the shape and porosity – not the size – of the iron oxide particles that determine the efficiency of green iron production. Their method uses saltwater and affordable, readily available iron oxide, submerged in an electrochemical cell where current drives a series of reactions.
These reactions separate oxygen from iron, leaving behind chlorine as a byproduct – a commercially valuable substance. The method not only eliminates fossil fuels in the production of metallic iron but also generates useful materials, making the process more sustainable and cost-effective.
Toward an economical green iron industry
“The goal,” said lab lead Kempler, “is not just to invent something that works, but to deliver a solution that’s sustainable, accessible, and significantly less harmful to the environment than current methods.”
Large-scale electrochemical plants require substantial investment. But if the input material allows faster iron production, it can dramatically reduce final costs.
The team believes other iron oxides with similar structures could also be effective, as long as porosity – and thus the reactive surface area – remains a priority.