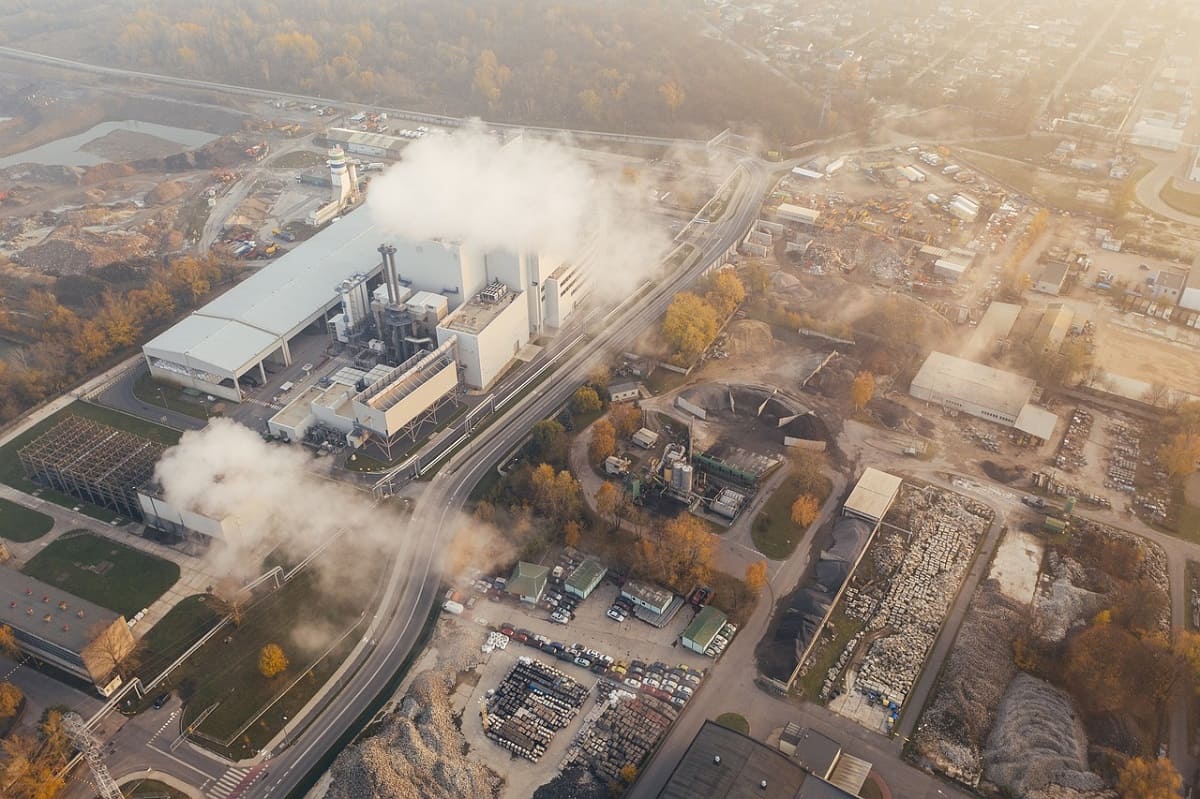
Industrial exhaust gases converted into consumer products
Shampoo, body wash, detergents, and even fuels made from industrial exhaust gases. It may sound futuristic, but a new study from the University of Surrey suggests it’s a viable pathway for reducing carbon emissions by turning waste into everyday goods.
Researchers argue that the carbon captured from industrial emissions could be transformed into high-value chemical compounds used in household products.
What can industrial exhaust gases become?
The study focused on a specific compound: AE7 ethoxylated alcohol, a high-value surfactant widely used in liquid detergents. It plays a key role as an emulsifier in everyday hygiene products like shampoos and body washes.
Traditionally, AE7 is produced by reacting fatty alcohols with ethylene oxide, mostly derived from fossil fuels and, to a lesser extent, from bio-based sources.
The research proposes a new production method using carbon extracted from exhaust gases released by paper mills and steel plants. In this model, captured CO2 is first reacted with hydrogen to produce syngas, then processed using enzymes to form alkanes. These alkanes are converted into fatty alcohols and finally into AE7 through a reaction with ethylene oxide.
Transforming CO2 into chemical ingredients
The process, led by professor Jhuma Sadhukhan, was analyzed through a full life cycle assessment. Results showed a significant environmental benefit: up to an 82% reduction in global warming potential (GWPP) for emissions from the paper industry, and nearly half that for steel plant emissions. The study evaluated the entire life cycle of converting waste gases into surfactants for essential consumer products.
“For decades, fossil fuels have underpinned manufacturing, not just as a source of energy, but also as a key ingredient in products people use daily,” said professor Jin Xuan, co-author of the study. “But that dependency has come at a steep environmental price. Our results show that CO2 waste can become part of the solution rather than part of the problem.”
Good for the planet, but not yet for the wallet
Despite the environmental promise, the study also highlights major economic barriers. The process remains expensive, largely due to the high cost and limited availability of hydrogen, both critical to CO2 conversion. The surfactant market is projected to reach $59.5 billion by 2032, yet the conversion process would require renewable energy to be sustainable due to its high energy consumption.
A separate study assessing the economic viability of different production methods found that CO2 capture costs about $8 per kilogram, more than double the $3.75 per kilogram cost of fossil-based methods. While environmentally advantageous, the process remains economically unfavorable.
Researchers emphasize that future technological advances and increased demand for sustainable products could shift the balance.
As noted in the study, “These findings will play a key role in shaping the future of sustainable chemical manufacturing. They will guide industries and provide critical recommendations to policymakers on accelerating the shift toward a circular carbon economy.”