China currently produces over three-quarters of the world’s batteries at prices up to 30% lower than Western competitors, but the market is evolving
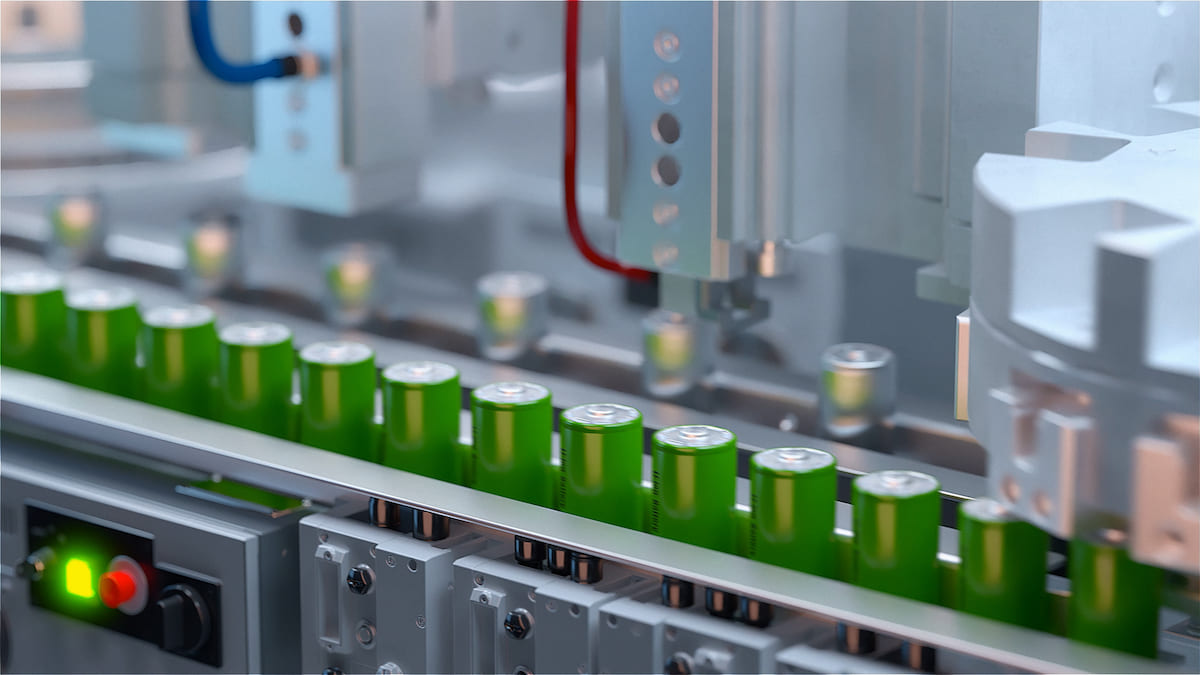
2024 has not only been marked by record price cuts in photovoltaic modules. The downward trend, driven by rising demand and overproduction, has also impacted the battery industry. This global shift has clear geographic roots, with China playing a dominant role. The country now manufactures over 75% of all lithium batteries sold worldwide, pricing them 20% to 30% lower than those produced in the U.S. or Europe.
However, the industry is undergoing significant changes, as highlighted in the International Energy Agency’s (IEA) new commentary, “The battery industry has entered a new phase.”
The global battery industry in numbers
This new phase is defined by two key trends: the shift from small, localized markets to large-scale, globalized production and the standardization of various technological approaches.
One thing is certain: the battery industry is growing at an unprecedented rate. By the end of 2024, global production capacity reached approximately 3 TWh per year – a figure that could triple within five years if all announced projects come to fruition. At the same time, prices have continued to drop. Thanks in part to lower raw material costs, the average price of an electric vehicle battery pack has now fallen below $100/kWh.
“Looking ahead, economies of scale, supply chain partnerships, production efficiency, and the ability to rapidly bring innovations to market will be crucial for competition,” analysts explain. “This is likely to result in further industry consolidation, as governments work to geographically diversify battery supply chains.”
China’s dominance in the battery industry
China’s leadership in rechargeable battery production is no secret. However, in 2024, the country further solidified its dominance, propelling the rise of major industry players such as CATL and BYD. These companies were among the first to rapidly scale production while optimizing efficiency, achieving higher yields than competitors.
This success has been facilitated by deep supply chain integration. Through acquisitions and strategic partnerships, many Chinese companies now control nearly every stage of the value chain—from raw material extraction to battery pack manufacturing. In the case of CATL and BYD, this integration extends even to electric vehicle production.
Additionally, “Chinese manufacturers have prioritized lithium iron phosphate (LFP) batteries, a more cost-effective chemistry,” IEA analysts note. “Initially considered unsuitable for electric vehicles due to lower energy density, years of research and development have significantly improved LFP technology. Today, LFP batteries account for nearly half of the global EV market, having more than tripled their market share over the past five years.”
The battery industry in Europe
China’s competitive pricing, combined with intense domestic competition, made Chinese batteries the most cost-effective option in 2024. This expansion has put significant pressure on European manufacturers. “Production costs in Europe are about 50% higher than in China, while the region’s battery supply chain remains relatively underdeveloped, and there is a shortage of skilled workers.”
However, there are signs of positive change. The IEA highlights two key trends: first, Chinese manufacturers are expanding their presence in Europe through partnerships; second, South Korean companies have begun investing in LFP battery production in the region. South Korea currently leads in overseas battery manufacturing capacity, producing nearly 400 GWh annually – far exceeding Japan’s 60 GWh and China’s 30 GWh outside its borders.
Meanwhile, Southeast Asia and Morocco are emerging as potential battery manufacturing hubs. “Southeast Asia has attracted significant Chinese investment, which could accelerate technology transfer and innovation. In Indonesia – home to half of the world’s extracted nickel – the first electric vehicle battery plants and graphite anode production facilities began operations in 2024.”