Researchers at the U.S. NREL have created a new resin for the production of wind turbine blades, made from biomass and capable of facilitating the upcycling of old blades.
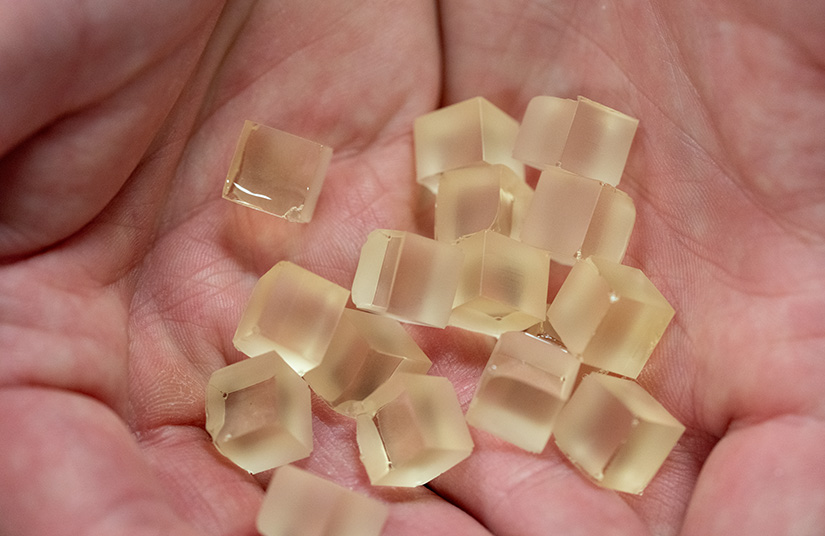
New wind turbines are being developed from biomass
The latest advancement in the field of “wind recycling” comes from the United States, specifically from one of the national Department of Energy laboratories. A group of scientists from the National Renewable Energy Laboratory (NREL) has worked on the ecodesign by creating innovative bio-derived Wind Turbine Blades. To be precise, there is only one derived material, but in the overall equation, it is one of the most important because it determines the mechanical strength of the components. Let’s talk about the resin that, along with the reinforcing fibers, is used in producing such components. But to understand the scope of the work done by NREL, it’s necessary to take a step back.
The thermosetting resins of wind turbine blades
Most modern blades in megawatt-scale wind turbines are produced using thermosetting resin systems such as polyester, vinyl ester, or epoxy reinforced with fibreglass or carbon, along with a custom adhesive for the internal reinforcement spars. Materials and structure give the blades the necessary lightness and strength, making recycling operations complex.
In other words, with current technology, the blades of wind turbines last about 20 years, after which – in the best-case scenario – they can be mechanically recycled. For example, grinding and milling them to use as a filler in concrete. Or by transforming them into skis and supports for photovoltaic modules. In the worst case, they are destined for incineration or landfill.
In recent years, however, new efforts in the wind sector to make turbine blades recyclable have opened up a new trend. Although the results are still limited and applied on a small scale, there is an emerging growing attention and interesting prospects.
Pale wind turbines made from bio-derived materials, the PECAN approach (PolyEster Covalently Adaptable Network)
The NREL study fits in in this context. Scientists have developed bio-derived wind turbine blades using an innovative thermosetting resin obtained from biomass. Nicknamed PECAN—an acronym for PolyEster Covalently Adaptable Network—this special resin would not only help extend the blades’ lifespan but could also be immediately adapted to current industrial processes.
“The PECAN approach for the development of recyclable wind turbine blades represents a fundamental step in our efforts to promote a circular economy for energy materials,” said Johney Green, associate director of the Mechanical and Thermal Engineering Sciences Laboratory at NREL.
PECAN was born from the desire to find a new way to facilitate the upcycling of wind turbine blades. The scientists wanted to create a blade that could be recyclable and began experimenting with a series of raw materials suitable for achieving this goal. But to their great surprise, they discovered that the innovative resin—developed using bio-derived sugars—achieved the goal and demonstrated performance comparable to traditional resins.
The advantages of PECAN resin
The team has built a 9-meter wind turbine prototype. Subject to validation testing, it has proven capable of maintaining its shape, resisting stress and weather conditions, and being produced in timeframes similar to the existing polymerization cycle used in the current manufacturing of modern blades. “Nine meters is a scale in which we were able to demonstrate all the same production processes that would have been used for the 60, 80, and 100-meter blades,” said Robynne Murray, the second author of the publication in Science.
Obviously, the other key element that characterizes the research is circularity. Biobased wind turbine blades can be chemically recycled with a mild thermal treatment that allows the individual components to be recovered and reused by the wind turbine industry. Closing the circle for good.